We’ve all had those moments where there’s a lot of work to do, we’ve got a method of doing it which takes time, but we persevere “because it works”, despite there being an easier, faster or more efficient solution just within reach.
Here at Selmach we refer to that as the “Square Wheels” problem. So often we hear from our customers the same two phrases: “I’m too busy to think about getting that new machine, maybe later once I’ve got less work on”
Then, when they have bought that new piece of machinery and got it in the workshop up and running; “I should have bought this years ago, it would have saved me so much time, energy and money!”
Here’s a few scenarios our customers regularly encounter, and the solutions that we’ve suggested for them:
- Cutting down tube, box and flat with an angle grinder
- Using a handheld plasma for repetitive cutting tasks or outsourcing profiling altogether
- Using a tape measure instead of a measuring system
- Using a manual machine to cut, roll or bend 1000s of repeat parts
- Using a mag-drill or pillar drill for punching out holes
- Notching tubes with an angle grinder / drill
- Using a sledgehammer to flatten out warped plate
- Thinking you can’t justify the cost of a new piece of machinery
If you’re worried about financing new machinery, fear not, we can guide you on purchasing via finance, spreading the cost over several years at a competitive rate.
Cutting down tube, box and flat with an angle grinder
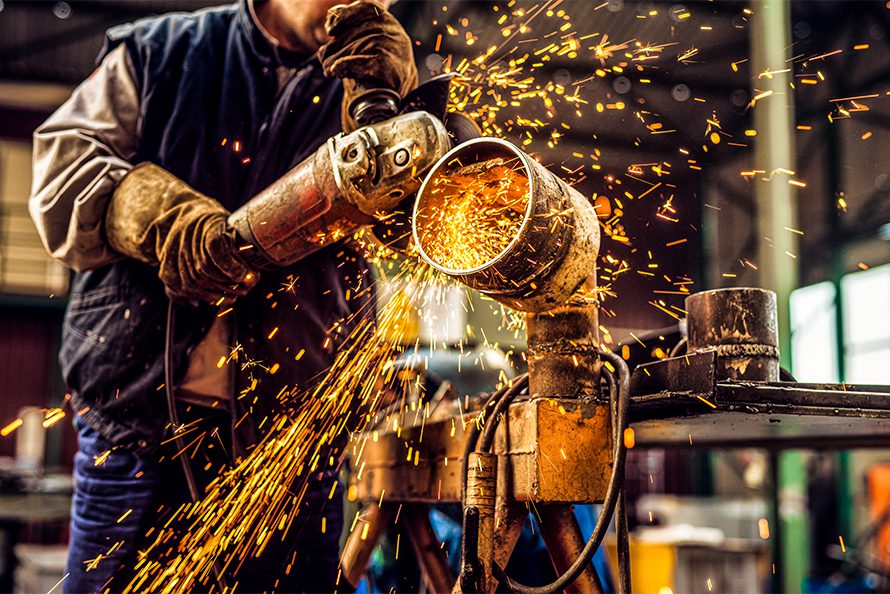
Smaller fabrication shops spend a lot of time using an angle grinder to cut lengths of material to size.
This can be time consuming, and inefficient, alternatives could be a Chop Saw (Circular Saw) or a Bandsaw.
With a gravity down-feed bandsaw, you can set-up the material to cut, freeing you up to carry on with other work while it makes that cut.
More advanced bandsaws from our semi-automatic and automatic range will not only cut the material to size, but the bow can return, and the material feed through and begin the next cut.
Using a handheld plasma for repetitive cutting tasks or outsourcing profiling altogether
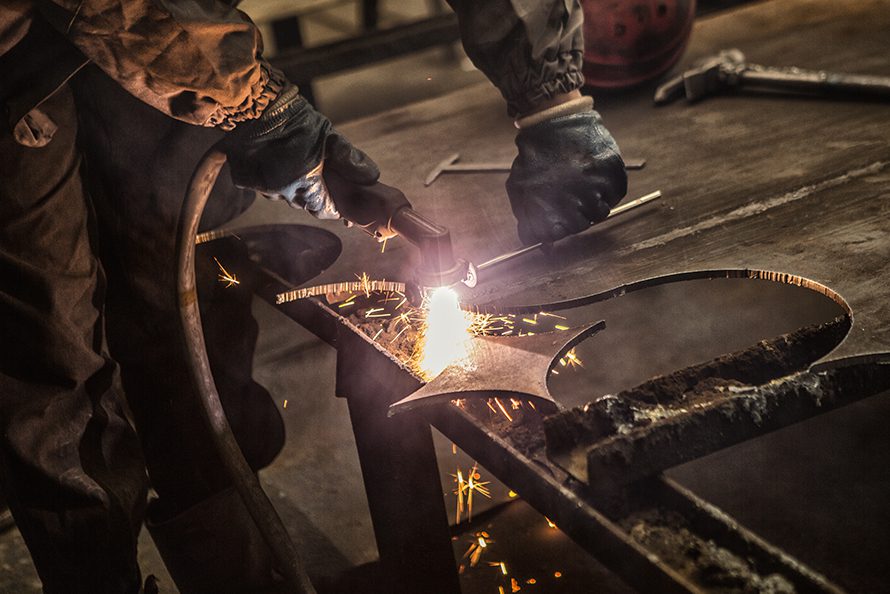
Handheld plasmas certainly have their place, especially when working on site, however all too often we see customers who are using them for repetitive cuts in the workshop, or customers who are spending £1000s on outsourcing each month.
A CNC Plasma Table may not be as expensive as you might think, and they can quickly pay for themselves, when you factor in the cost savings of bringing profiling in-house, not to mention reducing your over-reliance on third-parties, keeping you in control of your material, your supply chain and your timelines.
Using a tape measure instead of a measuring system
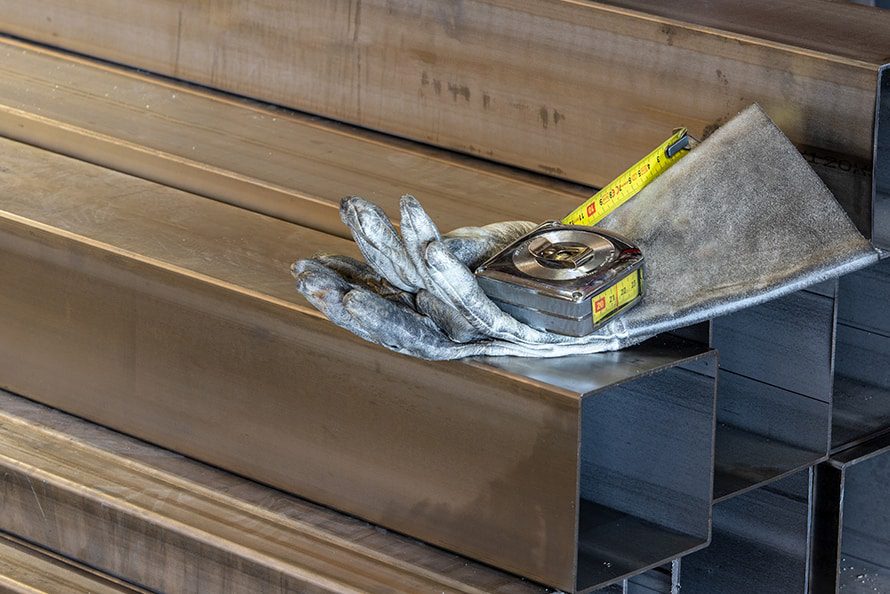
The trusty tape measure and marker, a quick and simple method, but not the most efficient. Have you ever wondered “Is there an alternative to using a tape measure for marking out metal?” There is! A measuring system on your roller track can make measuring a breeze, and improve accuracy, repeatability and efficiency no end.
Our range of Pehu LMS measuring systems will improve the accuracy of your measuring. Find out more about these on our website.
Using a manual machine to cut, roll or bend 1000s of repeat parts
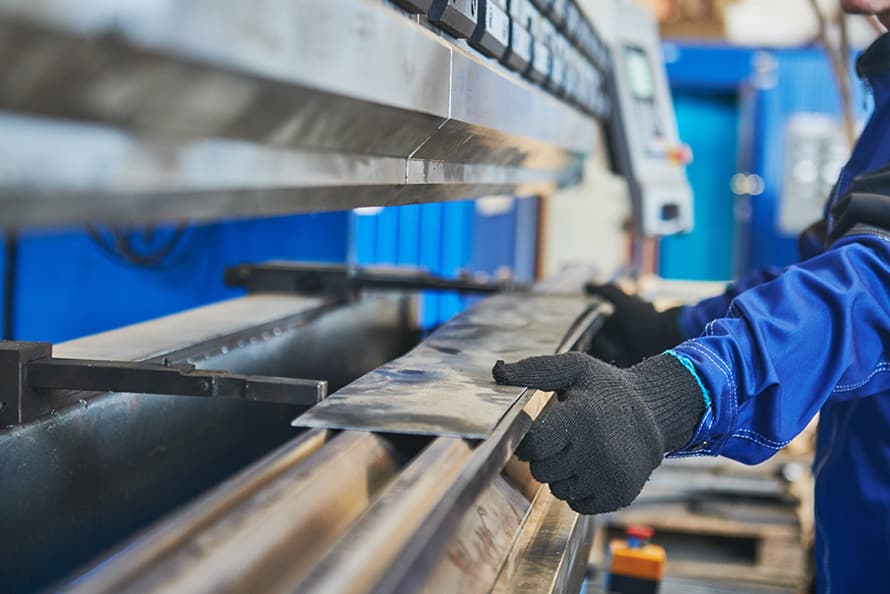
Manual equipment is brilliant for basic jobs, but once you’re reaching the point of repeating the same part 100s or 1000s of times, it’s time to think about CNC repeatability. Whether you’re cutting, bending, folding, automation will save you time, money and manpower.
An auto-feed bandsaw can be set up with roller track and material to feed in and be cut to length, allowing the operator to carry on with other tasks, or prep further automation machines. (One operator could have two automatic bandsaws running concurrently for instance)
Set-up time for any form of bending or folding is a big time sink, with CNC-enabled machines, you can have jobs pre-programmed, and swap jobs at the click of a button, coupled with the correct tooling for your needs, your process can be highly optimised for efficiency, saving you time and money in the long run.
Using a mag-drill / pillar drill for punching out holes
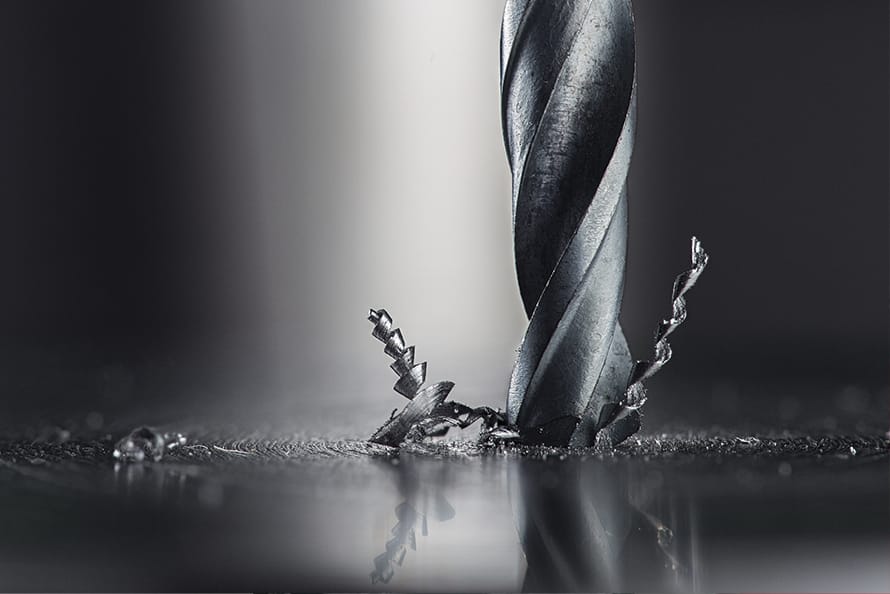
Cutting material to a specified size, and making holes in it is pretty much the process followed by every fabricator in the world, but could it be more efficient? Using a Mag-Drill or Pillar Drill for punching out holes is quite a manual process, a steelworker could speed that process up for you immensely.
Our Morgan Rushworth Steelworkers come with 5 different stations, including a notching and a punching station, allowing you to punch holes in material in seconds. With a wide range of punch and dies, including an assortment specialist tooling, these versatile machines can speed up your processes.
Notching tubes with an angle grinder / drill
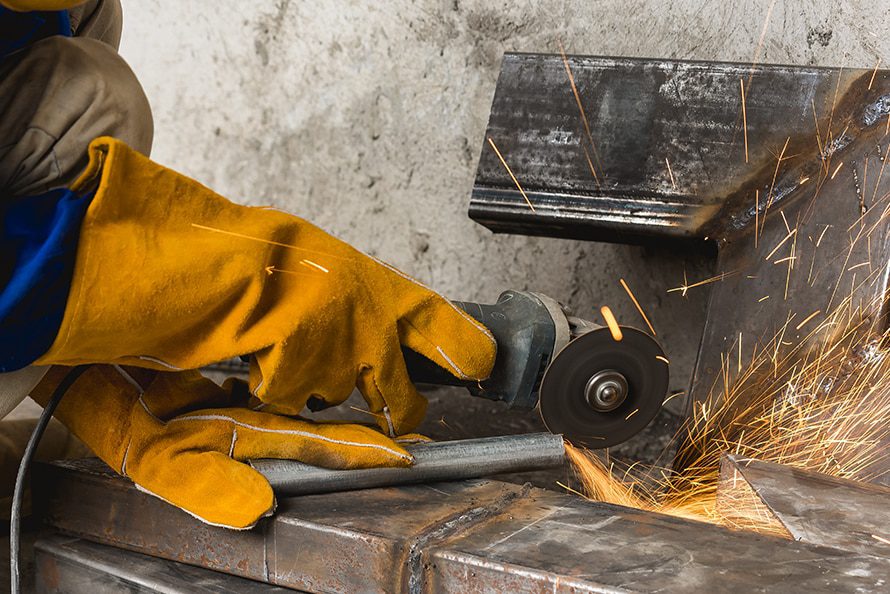
Using an angle grinder or drill to notch tubes and box section may seem like a quick and effective method, however when you’ve got a lot of parts to do, it can quickly become a time-consuming process.
Tube notchers offer a fast and efficient way of notching tubes ready for welding, taking seconds to do work that would take a lot longer with an angle grinder.
A Steelworker can also be a solution too, if you’re notching material ready for galvanising, a galv-v notching tool can punch out the notch ready for dipping into a galvanising bath, see our video on specialist punch and dies for our steelworker range below.
Using a sledgehammer to flatten out warped plate
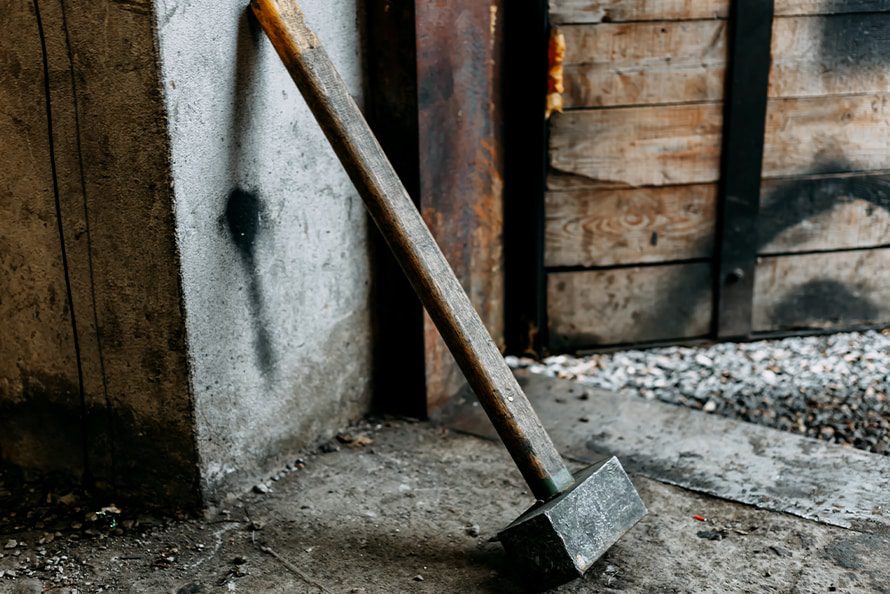
Nothing says metal bashing quite like using a sledgehammer to flatten out warped plate steel.
Clearly it’s not the most efficient method, and we’ve got a variety of different press machines that can assist you in flattening out warped material. Of course the benefit of these machines is they can also be used to put intentional bends and folds into material too, and with far more accuracy and repeatability than your sledgehammer.
We’ve got an entirely separate blog on this topic, which you can view here. The main solutions though are using sheet rolls or section rolls to roll material back to the desired profile, or flattening material with either a H-Frame Press or a Horizontal Bending Press.
Thinking you can’t justify the cost of a new piece of machinery
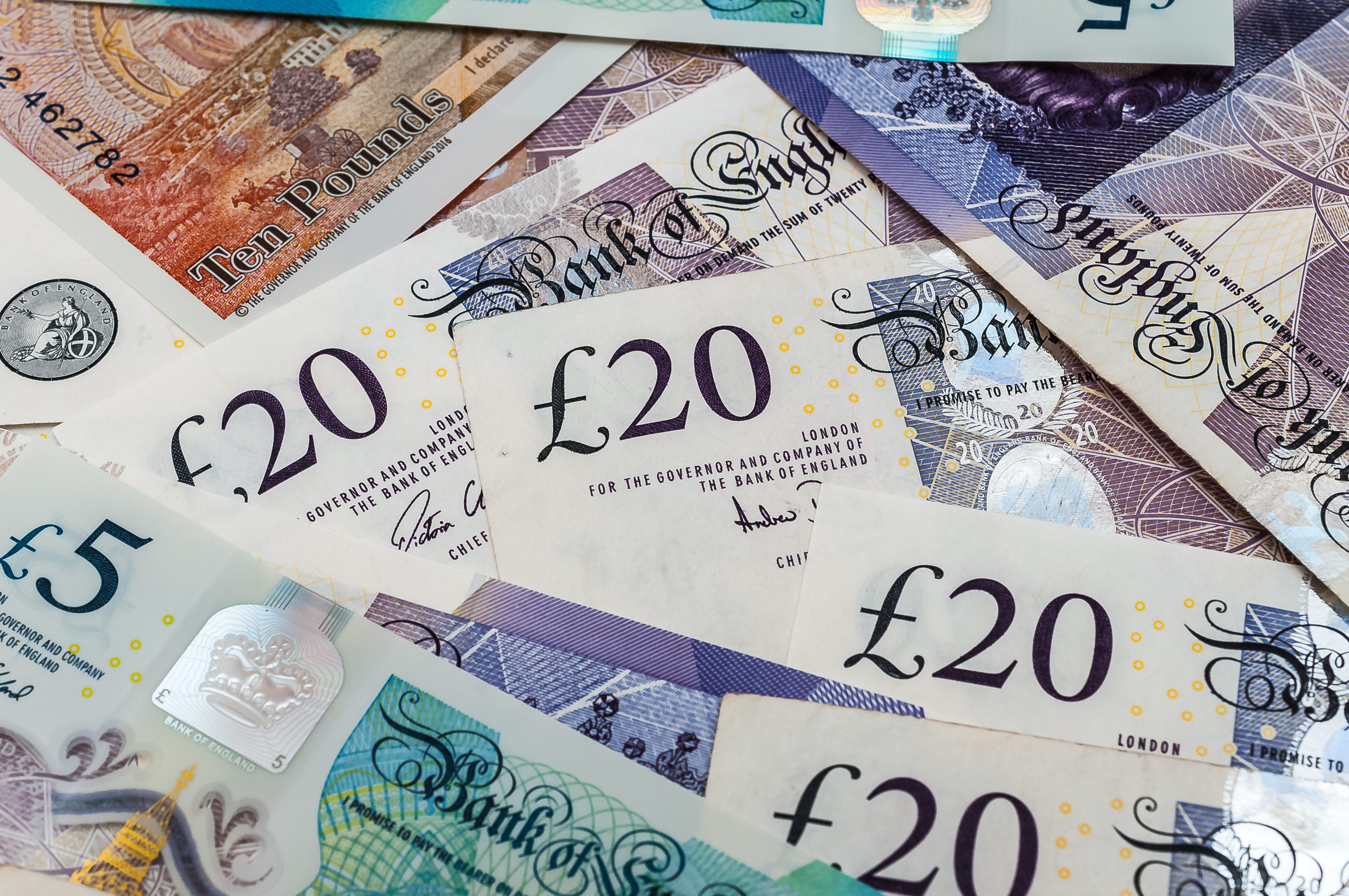
It can be difficult to justify a new machine, especially if it’s only for a one-off job at this point in time. You’ve got the costs to consider, the space it’ll take up in the workshop, training operators to use it etc. However, thinking in the long-term, new machinery can open up new options and opportunities for your business to deliver new services and products.
Large ticket items are especially scary to make the leap and purchase, however they can also be the biggest catalysts for growth for your business. Buying your own high-definition CNC plasma to save on outsourcing could not only pay for itself in a matter of months, but if you’ve got spare capacity on the machine, you can provide that capacity to other fabricators in your area.
We’ve had multiple customers who have purchased one of our Plasma machines, and been inundated with offers of work as soon as local companies find out that they’ve got one. One of our customers who bought a plasma said their business went from £100,000 a year to £1,000,000 a year in the space of 12 months!
If you’re currently facing a process within your business that is taking a lot of time up, speak to our sales team, they can advise you if there’s a better, or more efficient method of doing it, with our extensive range of machinery. Don’t let the square wheels slow your business down!
Speak to us on 01432 346 580 or email [email protected]
Worried about financing new machinery?
Committing to new machinery can seem daunting, especially if it’s a sizeable proportion of your current income. However, time and time again our customers say how the machines they’ve purchased from us have paid for themselves within months. Especially large machinery like Plasma machines, where the cost of outsourcing has been a large expense, these machines have paid for themselves within 6 months!
There has never been a better time to look into capital expenditure.
We work with Finance Companies to help support a lot of our customers to make purchases for machinery – where payments can be spread out across a variety of time periods, for ultimate flexibility, at competitive interest rates.
Last Updated 15th May 2024
Published 12th October 2021