Morgan Rushworth HST Hydraulic Steelworker 415V
HST hydraulic steelworkers are equipped with standard tooling, including repetition support tables at the punch, shear, and notch stations. All five workstations feature adjustable hold-downs and comprehensive safety guards for safe operation. Twin operator functionality allows one shielded foot control to activate the punch and cylinder, while another operates the shear and cylinder. Accurate power inching enables precise tool setting and positioning, with the machine stopping safely at any position.
All models are fitted with a 1m auto-crop length stop complete with a ruler and LED lighting at every station. The HST range excels in delivering exceptional power and accuracy, while the HSW series focuses on maximising efficiency and meeting the demands of high-volume production.
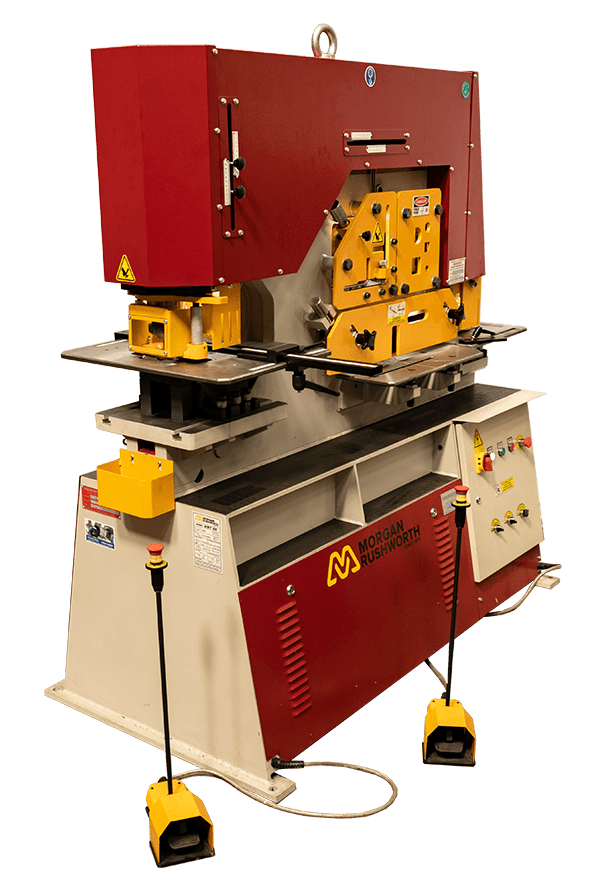
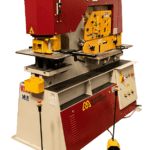
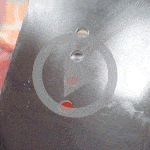
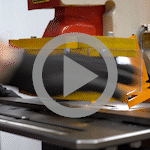
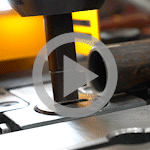
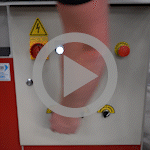
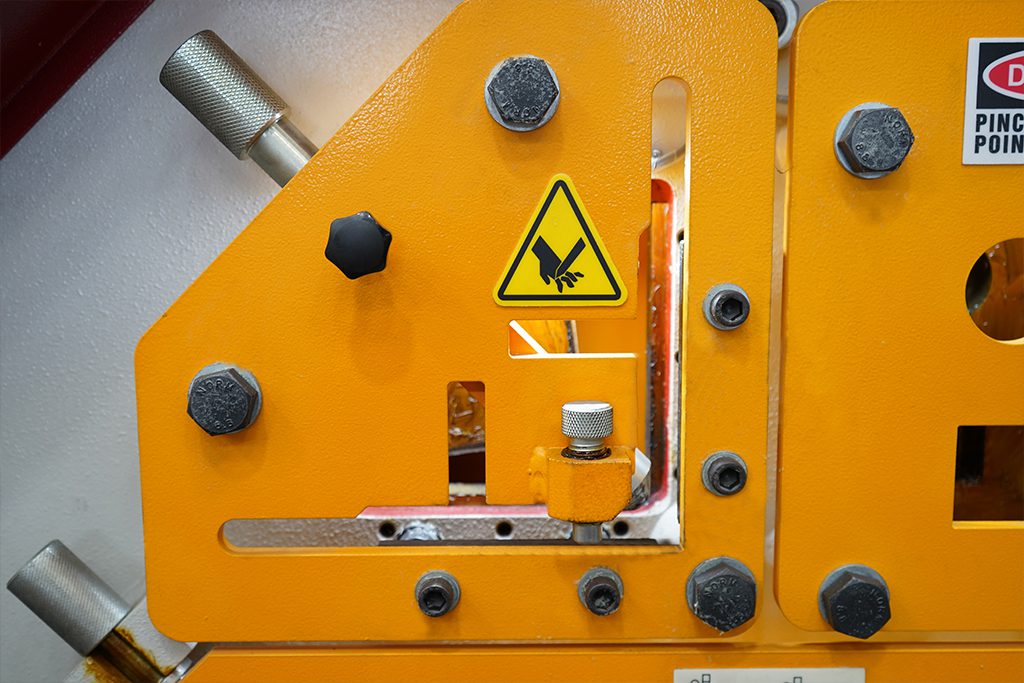
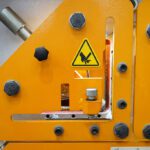
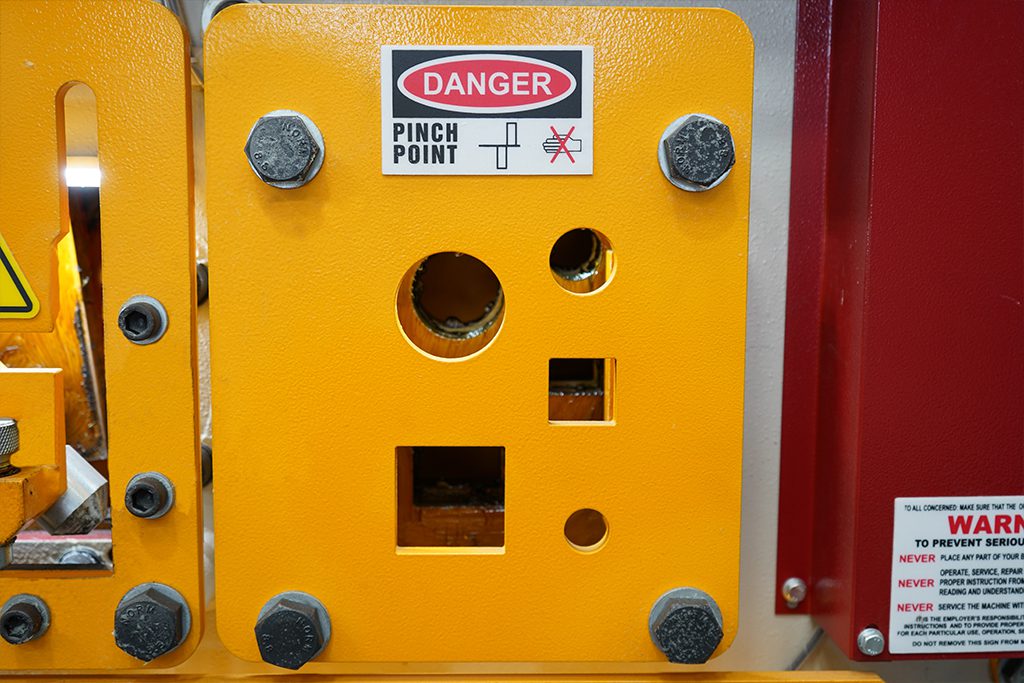
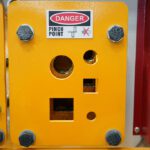
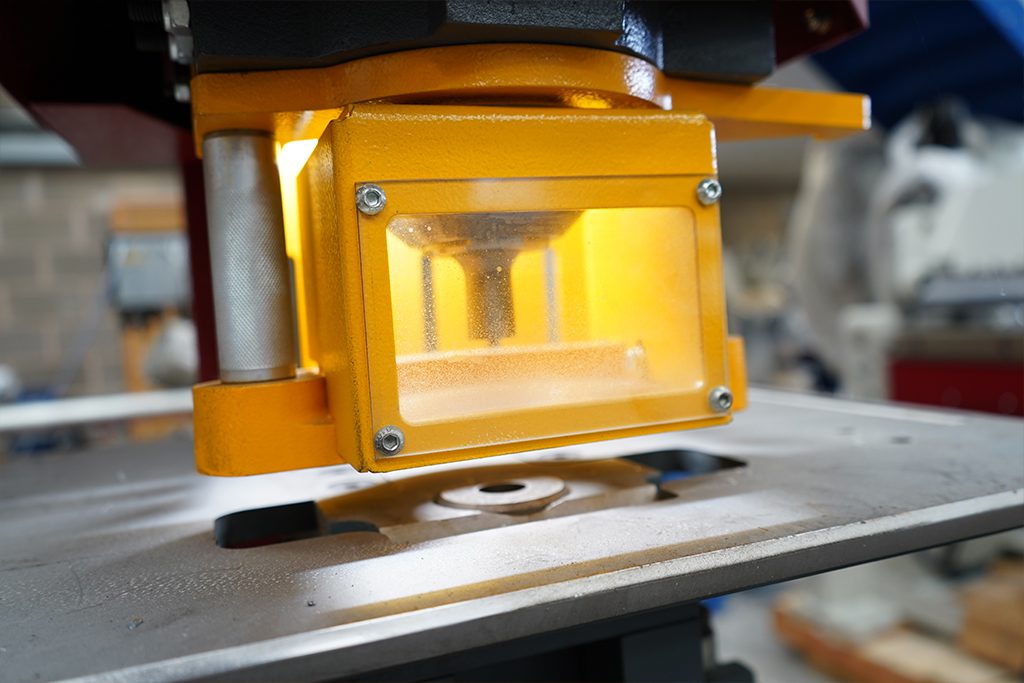
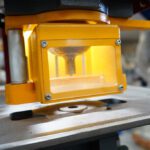
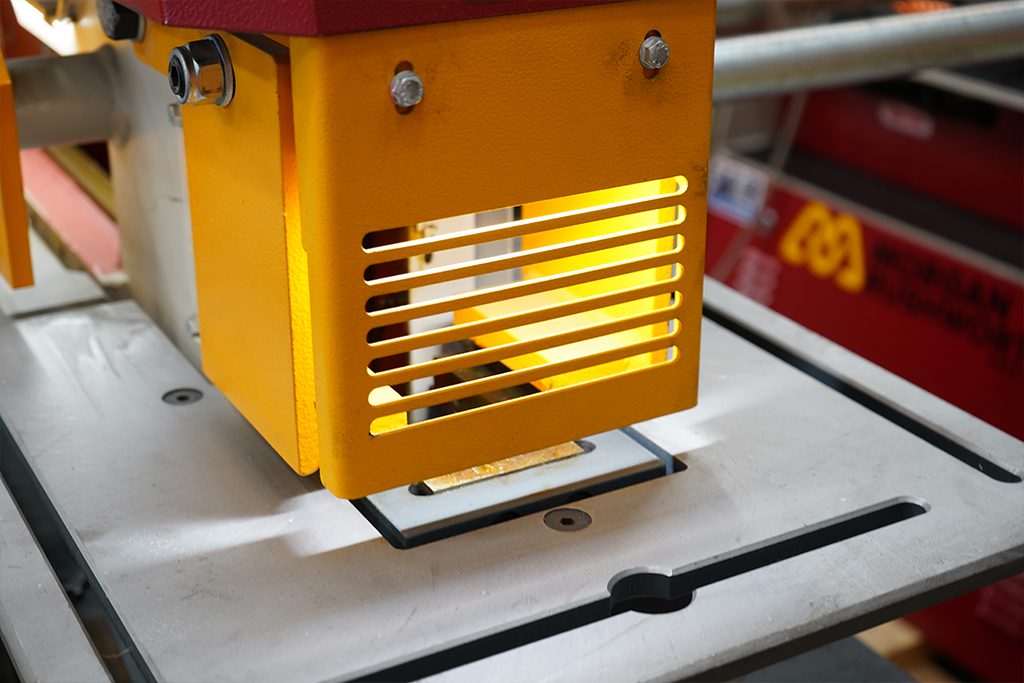
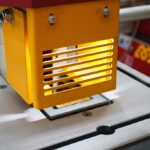
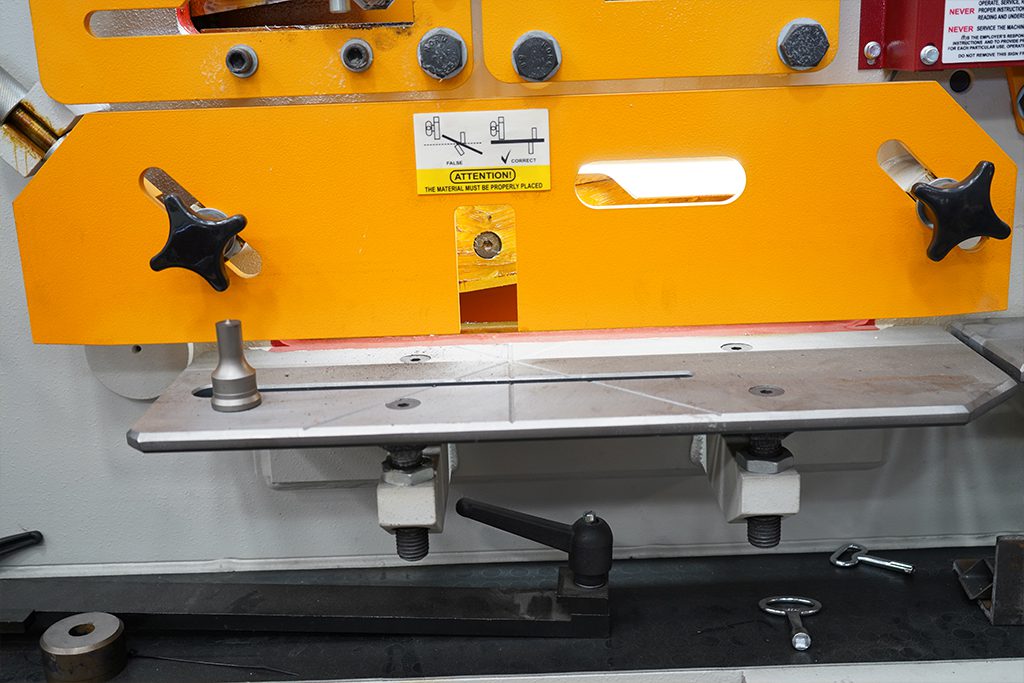
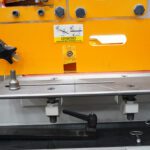
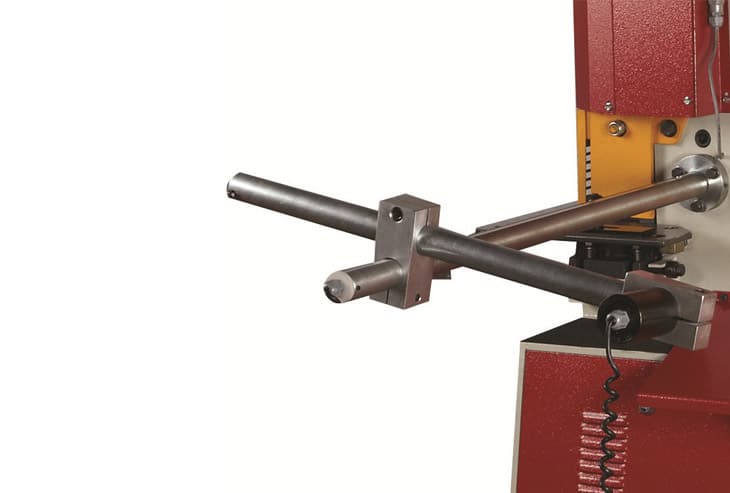
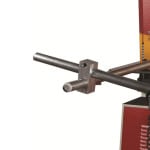
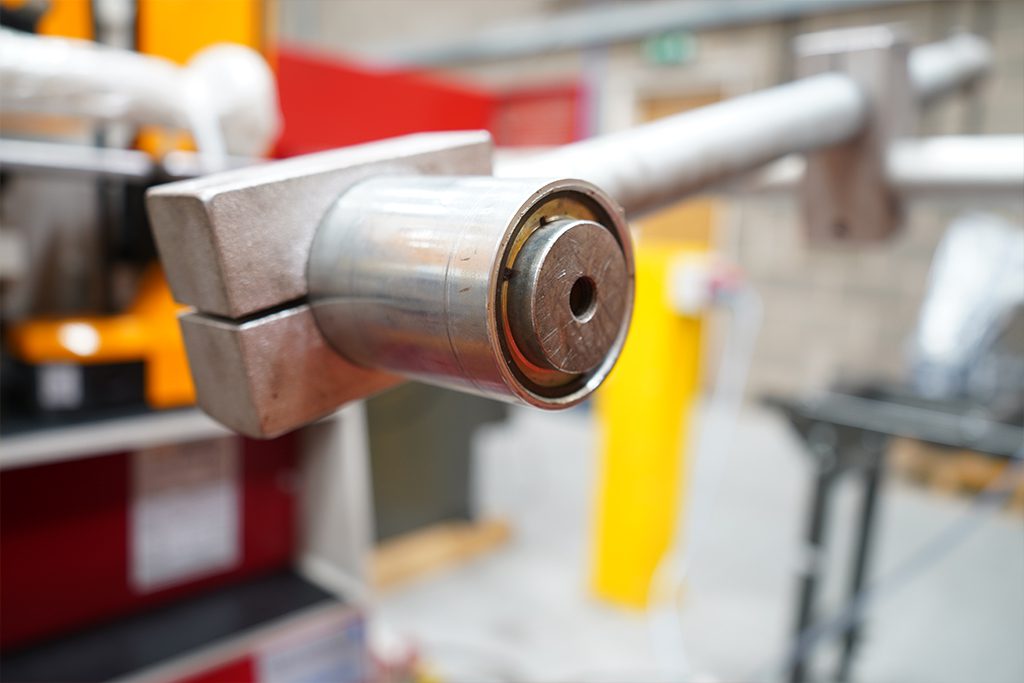
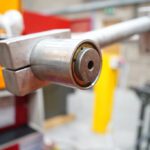
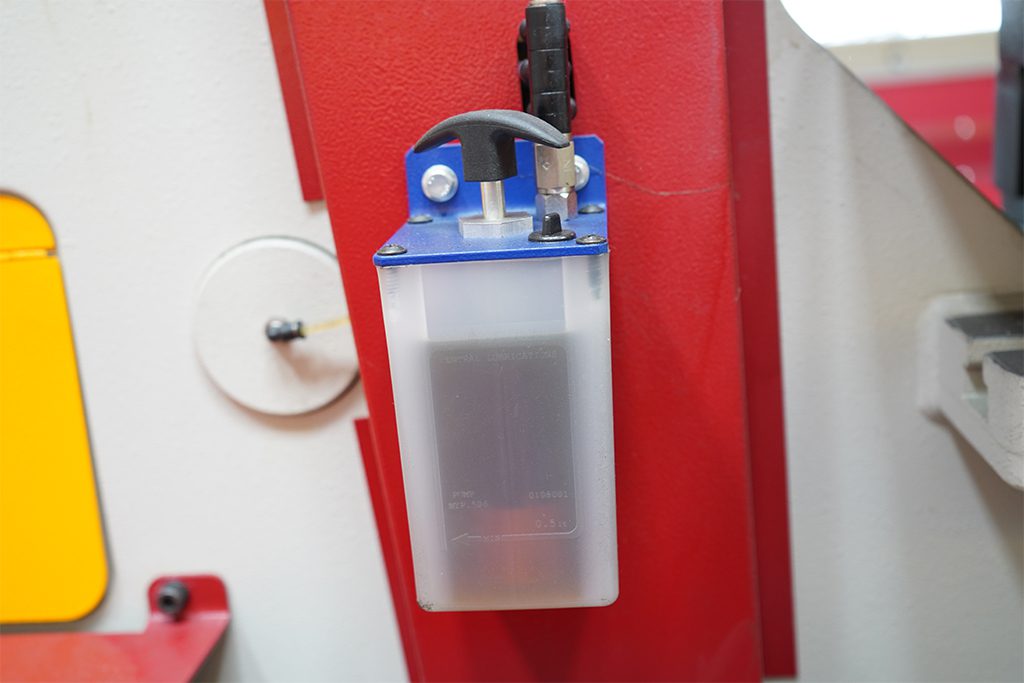

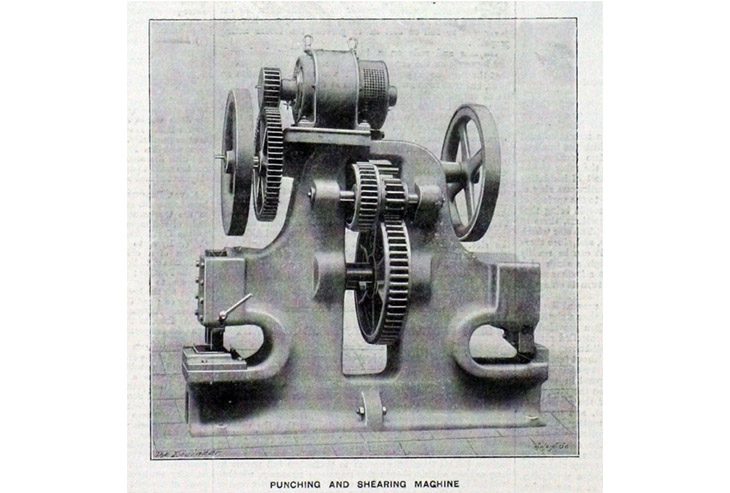
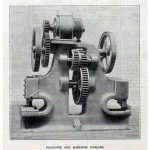
MODEL | HST 70 | HST 95 | HST 125 | HST 175 | |
STOCK CODE | M9003 | M9004 | M9005 | M9006 | |
PUNCHING | |||||
Diameter x Maximum Thickness | mm | 26 x 20 | 33 x 20 | 35 x 25 | 40 x 32 |
Maximum Diameter x Thickness | mm | 57 x 10 | 57 x 12 | 57 x 16 | 57 x 22 |
Stroke Length | mm | 55 | 80 | 80 | 80 |
Throat Depth | mm | 305 | 355 | 355 | 625 |
Largest Hole Diameter – Standard | mm | 38 | 57 | 57 | 57 |
Largest Hole Diameter – Optional | mm | 160 | 160 | 225 | 225 |
SHEARING | |||||
Flat Bar – Width x Maximum Thickness | mm | 300 x 20 | 380 x 20 | 380 x 25 | 380 x 30 |
Flat Bar – Maximum Width x Thickness | mm | 375 x 15 | 480 x 15 | 600 x 15 | 600 x 20 |
Angle Flange Trim – max 45° | mm | 100 x 15 | 120 x 15 | 120 x 15 | 120 x 15 |
ANGLE CUTTING | |||||
90° Cut | mm | 130 x 13 | 150 x 15 | 150 x 18 | 200 x 20 |
45° Mitre (true int./ext.) | mm | 70 x 10 | 80 x 8 | 80 x 10 | 80 x 10 |
SECTION CUTTING | |||||
Round/Square | mm | 45 | 50 | 55 | 65/55 |
Channel/Beam – (Optional) | mm | 120 x 58 | 160 x 74 | 200 x 100 | 300 x 125 |
Tee – (Optional) | mm | 90 x 11 | 100 x 11 | 120 x 12 | 150 x 15 |
NOTCHING | |||||
Material Thickness | mm | 10 | 13 | 13 | 16 |
Width – Rectangle | mm | 45 | 52 | 60 | 60 |
Depth – Rectangle | mm | 90 | 100 | 100 | 100 |
Depth – Vee | mm | 60 | 70 | 80 | 80 |
TUBE NOTCH (OPTIONAL) | |||||
Maximum Outside Diameter | mm | 83 | 108 | 108 | 165 |
BENDING (OPTIONAL) | |||||
Bar Bending – Maximum Capacities | mm | 250 x 13 | 250 x 20 | 250 x 22 | 250 x 25 |
Sheet Bending – Maximum Capacities | mm | 500 x 3 | 500 x 3 | 700 x 3 | 700 x 4 |
TECHNICAL DATA | |||||
Motor Power | kW | 5.5 | 7.5 | 11 | 11 |
Weight | kg | 1620 | 2430 | 3080 | 6000 |
Length | mm | 1700 | 1920 | 2040 | 2730 |
Width | mm | 710 | 790 | 800 | 1120 |
Height | mm | 1800 | 1910 | 2030 | 2160 |
based on material strength of 450 N/mm2 |
Features
- Built-in LED Lighting System
- Twin operator hydraulic system with foot pedal control for the punching station independent of the shearing and notch stations
- Punch station featuring vertical ram action with fully adjustable ram stroke.
- Large punch station table with adjustable backgauge
- Low power inching for tool alignment
- Angle station for cropping angle iron at 90° or at 45° with either internal or external mitres
- Section cutting station for cropping round and square bar
- Shear station for cutting both thin and thick material without requiring blade gap or cutting angle adjustment. Can also be used for cropping the leg of angle iron and chamfering the ends of small flat bars
- 1 metre auto crop ruled length stop covering all cropping/shearing stations for repetitive work
- Notching station with rectangular notch tooling
- Centralised lubrication system
- Comprehensive safety guards
Options
- Tooling for special applications
- Flat bar bending unit at notch end
- Flat bar bending unit at punch end
- Minimum Deform Stripper Assembly
Morgan Rushworth HST Hydraulic Steelworkers
The Morgan Rushworth HST hydraulic steelworkers are designed to deliver exceptional power, precision, and safety for high-demand industrial applications. With standard tooling, including repetition support tables at the punch, shear, and notch stations, these machines cater to a variety of metalworking tasks while ensuring consistent performance and operator safety.
Versatile Five-Station Design
The HST hydraulic steelworkers feature five workstations, each engineered for specific operations such as punching, shearing, and notching. Adjustable hold-downs are installed at every station to securely control materials during processing, ensuring accuracy and reducing waste. This versatility makes the HST range suitable for a wide range of industrial tasks, from custom fabrications to high-volume production runs.
Twin Operator Functionality
The twin operator design is a standout feature of the HST range, allowing two operators to work simultaneously. The hydraulic system is activated by two shielded foot controls: one controls the punch and cylinder, while the other manages the shear and cylinder. This dual-control system enhances productivity by enabling simultaneous operations, while also maintaining safety through shielded controls.
Safety as a Priority
Comprehensive safety guards are fitted as standard on all workstations, providing a secure barrier between operators and moving parts. This focus on safety ensures compliance with workplace regulations and reduces the risk of accidents. Additionally, the machines include accurate power inching, allowing operators to stop the machine at any position for precise tool setting and workpiece alignment. This feature enhances both safety and accuracy during operation.
Precision Engineering
The Morgan Rushworth HST steelworkers are built with precision in mind. The hydraulic system provides accurate power inching to all five workstations, enabling fine adjustments for exacting tasks. The system’s ability to stop at any position further enhances accuracy, particularly for repetitive operations requiring consistent results. This level of precision ensures that the HST range meets the demands of industries requiring high-quality output.
Standard Features and Accessories
Every HST machine is equipped with a 1m auto crop ruled length stop, simplifying the cropping process and ensuring consistent material measurements. LED lighting is fitted at all five stations, providing clear visibility for operators and improving accuracy during operation. These standard features, combined with the robust design of the machines, make the HST range a reliable choice for diverse metalworking applications.
Durability and Maintenance
The HST steelworkers are constructed with durability in mind, featuring high-quality materials and engineering that ensure a long working life. The machines include a centralised lubrication system, which simplifies maintenance and reduces downtime. This easy-to-use system ensures that the machines remain in optimal working condition, even in demanding industrial environments.
Selmach Machinery’s Steelworker Range
Selmach Machinery offers two distinct steelworker ranges to meet varying operational needs. The HST range is designed for twin operation, providing enhanced power and precision for complex tasks. In contrast, the HSW range features single foot pedal operation, focusing on efficiency and high-volume production. With models ranging from 60 to 175 tonnes, Selmach’s steelworkers cater to a wide array of industrial requirements, ensuring the right solution for every workshop.
Applications and Industries
The versatility and robust performance of the HST steelworkers make them suitable for a range of industries, including:
- Construction: Fabricating structural components and reinforcements.
- Metal Fabrication: Producing customised metal parts with precision.
- Manufacturing: High-volume production of metal components.
These machines excel in applications requiring reliable performance, safety, and efficiency, making them a valuable asset for businesses looking to enhance their metalworking capabilities.
Key Features at a Glance
- Five Workstations: Includes punching, shearing, and notching capabilities.
- Twin Operator Design: Enhances productivity with dual shielded foot controls.
- Adjustable Hold-Downs: Ensure material stability and safety.
- Comprehensive Safety Guards: Fitted as standard for all stations.
- Accurate Power Inching: Allows precise tool setting and alignment.
- 1m Auto Crop Ruled Length Stop: Simplifies cropping and ensures consistent results.
- LED Lighting: Provides clear visibility at all stations.
- Durable Construction: Ensures long-term reliability and performance.
Why Choose Morgan Rushworth HST Steelworkers?
The Morgan Rushworth HST hydraulic steelworkers are engineered to deliver unmatched performance, safety, and versatility. Their twin operator functionality, combined with robust safety features and precision engineering, makes them a top choice for industrial workshops. These machines are designed to handle the demands of high-volume production while maintaining accuracy and ease of operation.
By choosing the HST range, businesses can benefit from increased productivity, reduced downtime, and a lower total cost of ownership. Selmach Machinery’s commitment to quality ensures that every steelworker is built to the highest standards, providing reliable performance and value for years to come.
Quick Start – Morgan Rushworth HST 95 Steelworker
12th November 2024 by Dave Hargest
How to Safely Remove and Install A Punch & Die on a Morgan Rushworth Steelworker
21st July 2017 by Clare Harris
HSP CNC Punch Vs Traditional Steelworker
3rd April 2017 by Clare Harris
How to Adjust the Stroke Limit Switches on a Steelworker
28th June 2016 by Clare Harris
How to Adjust the Material Clamping System on a Steelworker FAQ
15th June 2016 by Clare Harris
Related Case Studies
Coleg Gwent – Machinery for the next generation
14th November 2023 by Dave Hargest
Coleg Gwent is Wales' largest further education and one of the best-performing colleges, delivering a wide range of part-time and full-time academic and vocational courses to over 16,000 students annually... More
Pembrokeshire College adds to their collection
26th April 2023 by Dave Hargest
Pembrokeshire College is a provider of a wide range of Post-16 study options in South-West Wales, including an impressive set-up for Engineering based courses with their new Welding and Fabrication.. More
Facade and Cladding Solutions expand and upgrade their machinery
22nd June 2022 by Dave Hargest
Our customer Facade and Cladding Solutions spoke to us about their experiences buying a range of machines from us here at Selmach, including a Press Brake, Guillotine, Steelworker and Corner.. More
Ornamental blacksmith Stow Forge takes it easy with the Morgan Rushworth Steelworker
6th August 2020 by Clare Harris
Stow Forge is a family-owned ornamental blacksmiths and metal fabrication business. They are based in Essex and provide Colchester, Chelmsford and the surrounding areas with high quality hand-crafted domestic products.. More
T&M Buildings go better & faster by upgrading to the Morgan Rushworth Steelworker
6th July 2020 by Clare Harris
T & M Buildings specialises in the design, fabrication, supply and erection of bespoke steel frames for farm, agricultural and industrial clients, covering Devon and the surrounding areas. When they.. More