Facade and Cladding Solutions, based near Stevenage, are suppliers of all manner of Facades, Cladding, Soffits and sheet metal products for buildings. We spoke to Stephen Sawyer, Factory Manager about their recent installation of a Morgan Rushworth PBS 3100/120 Pressbrake, HSGS 3100/6 Guillotine, HSW 60 Steelworker and an RVD 220/6 Corner Notcher.
“Would I recommend you and your machinery? 100%, definitely, everyday. 10 out of 10 from start to finish.”
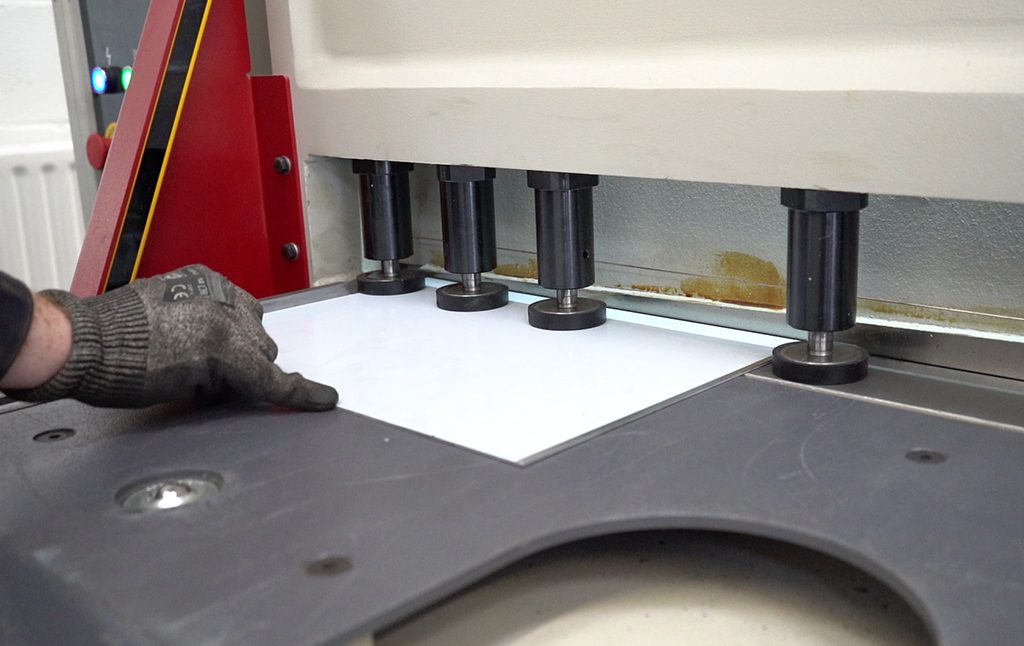
What was the reason(s) that the business considered this machinery in the first place?
We were looking to expand into a new manufacturing factory, and wanted to replace our existing machinery with new.
How did you hear about Selmach and why did you choose them?
I bought an Ajan Plasma from Selmach around 7 or 8 years ago in a previous role, and the service had been outstanding, so I made contact with Hugh Bushnell to see how they could help again.
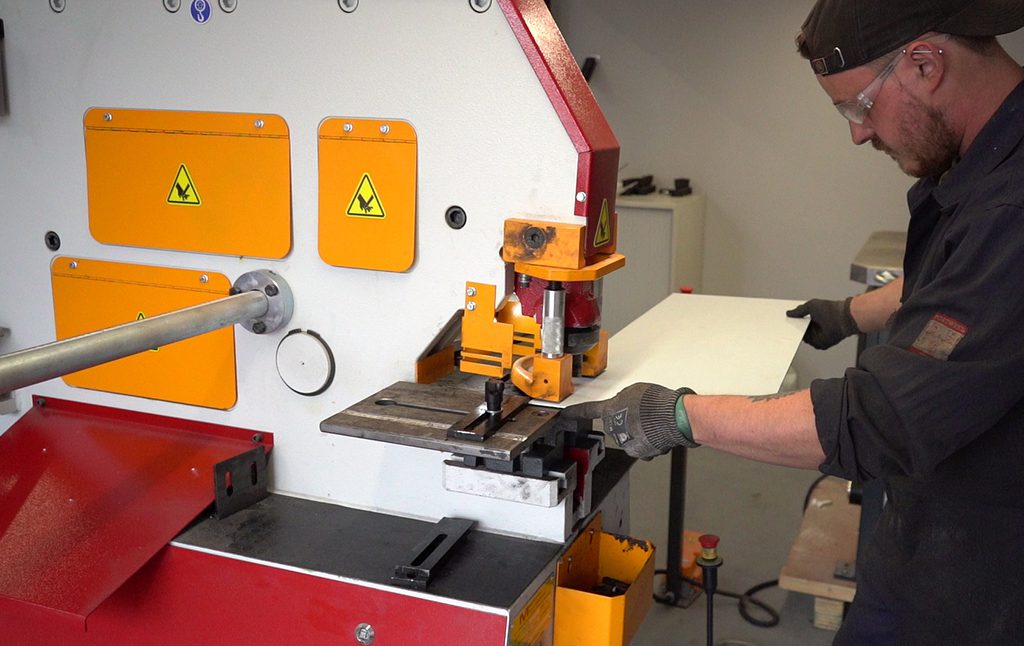
What machinery have you purchased from Selmach Machinery to solve that?
We’ve added a Morgan Rushworth PBS 3100/120 Pressbrake, Morgan Rushworth HSGS 3100/6 Guillotine, Morgan Rushworth HSW 60 Steelworker and an RVD 220/6 Corner Notcher.
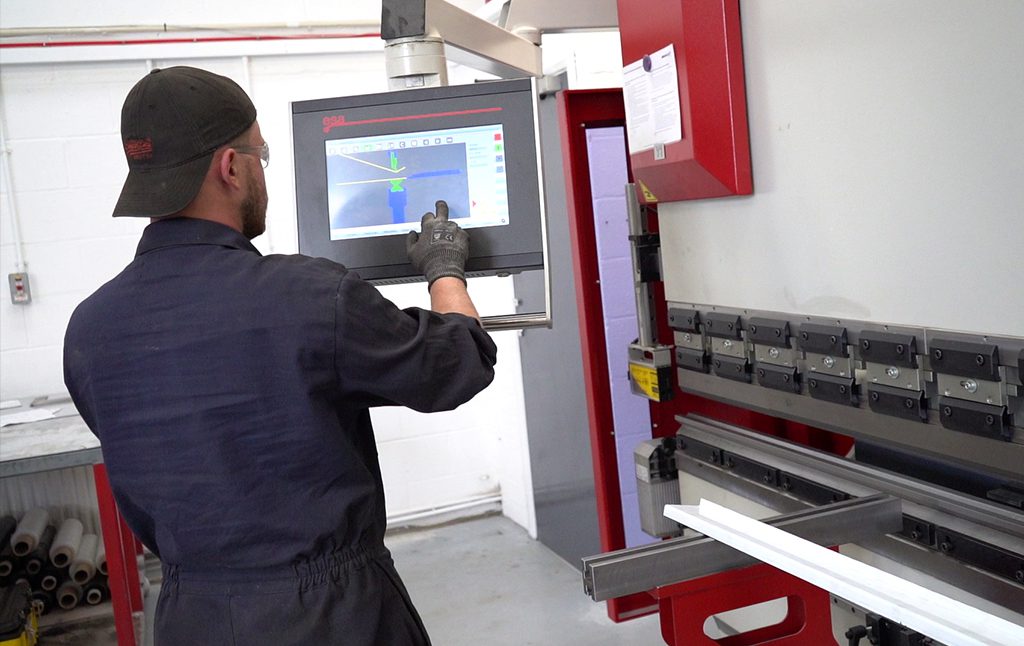
How has the machinery worked for yourselves?
We’ve only been in full production for a couple of weeks, but it’s been such an improvement. On our other, older machines even the simplest of tasks used to take so much time to do, now it’s much faster for us.
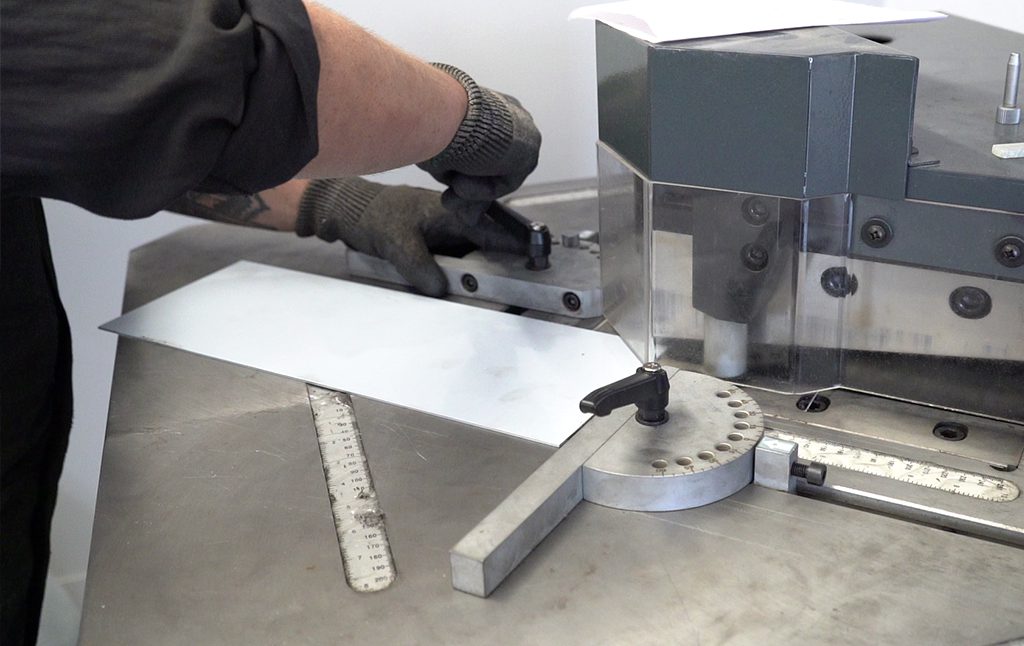
How was the experience with Selmach while you were being quoted / advised and delivered?
My experience with Selmach has been excellent. They helped guide me through what machine would work with us, as I was looking at initially a 4m machine, or a bit bigger. But they advised me to go to a 3m machine. So again it worked out better as it was not only cheaper, but more importantly it works in the factory where we are at the moment, it gave us that little bit more room. The best thing that worked with us was the delivery, we weren’t having to wait 3, 4 months, we got it, which was very demanding of ourselves, we got it within a 6-7 week time frame. And then when it was due to be delivered, we had issues with our factory in the handover period. We had to delay it by two weeks which Selmach, again, had no issues with, they worked with us to get the machines in when we were able to.
What about aftercare and service?
The aftercare from Selmach has been really good. I haven’t got a bad thing to say about the aftercare, anything we need we can WhatsApp the engineers, and you get a response within the house. Solutions, anything we need, repairs, they’re straight out.
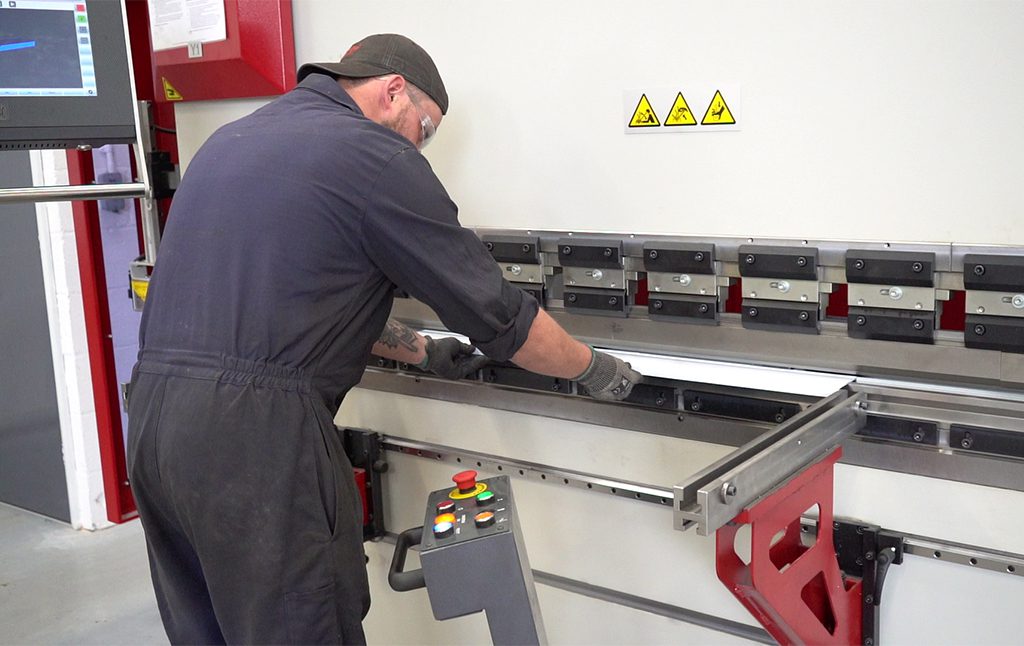
Any future machinery considerations?
Looking ahead, there will certainly be more machines purchased from Selmach. When we expand again, we’ll be looking at getting another guillotine and press brake. But hopefully things like a laser machine or even purchasing an Ajan plasma like I purchased 7 / 8 years ago, certainly something along those lines.
Would you recommend Selmach and our machinery?
Would I recommend you and your machinery? 100%, definitely, everyday. 10 out of 10 from start to finish.
If you’d like to find out more about our range of machinery, click the links below.
Published 22nd June 2022